Structural Principle and Performance of Double Plate Butterfly Check Valves
Jul 21, 2023
The double plate butterfly check valve is also a swing check valve, but it is a double-disc valve that closes under the action of a spring. The fluid from bottom to top pushes the valve disc apart. The valve has a simple structure, and the wafer is installed between two flanges, with small dimensions and lightweight. As shown in Figure 1.
Figure 1 Double plate butterfly check valves
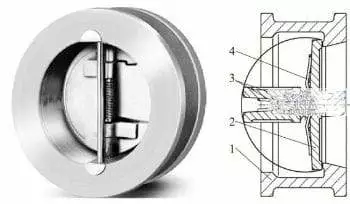
Figure 1 Double plate butterfly check valves
1. Valve bodies 2. Plates 3. Pin shafts 4. Springs
The double plate butterfly check valve has two spring-loaded D-shaped discs, which are placed on the rib shaft across the through hole of the valve. This structure shortens the moving distance of the center of gravity of the disc. Compared with the single disc swing check valve of the same size, this structure also reduces the weight of the disc by 50%. This valve reacts very quickly to reverse flow due to the spring load.
The double plate light structure of the double plate butterfly check valve makes the seat sealing and operation more effective. The long-arm spring of the double plate butterfly check valve enables the disc to open and close without rubbing against the valve seat, and the spring acts independently to close the disc (DN150 and above). The hinge support sleeve of the double plate butterfly check valve reduces friction and minimizes water hammer when stopped by the independent disc with bigger sizes.
Compared with conventional swing check valves, double plate butterfly check valves are generally stronger, lighter, smaller, more efficient, and less expensive. This valve complies with the API 594 standard. For most diameters, the face-to-face size of this valve is only 1/4 of that of conventional valves, and its weight is 15% to 20% of conventional valves, so it is cheaper than swing check valves. It is also easier to install between standard gaskets and pipe flanges. Since it is easy to handle and requires only one set of flange connection bolts, it also saves parts during installation, saving installation costs and daily maintenance costs.
The double plate butterfly check valve also has special structural features, which makes this valve a high-performance non-impact check valve. These features include no-clean opening, independent spring for most valves, and independent disc support systems. Some check valves do not have these features. Double plate butterfly check valve can also be designed with lugs, double flanges and extended valve bodies.
1. Opening and closing processes
The opening and closing process of the double plate butterfly check valve is shown in Figure 2.
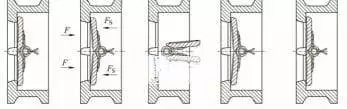
Figure 2 Opening and closing processes of the double plate butterfly check valve
The double-disc structure adopts two spring-loaded discs (half discs), suspended from a central vertical hinge pin. When fluid flows, the disc opens under the resultant force (F) acting on the center of the sealing surface. The acting point of the reacting spring support force (FS) is located outside the center of the disc face, causing the root of the disc to open first. This avoids friction of the sealing surface of the conventional valve when the disc is opened, and eliminates the wear and tear of the components.
When the flow rate slows down, the torsion spring reacts automatically, so that the disc closes and approaches the valve seat of the valve body, reducing the closing stroke distance and time. When the fluid flows backward, the valve disc gradually approaches the valve seat of the valve body, and the dynamic response of the valve is greatly accelerated, which reduces the influence of the water hammer, thereby achieving nonimpact. When the valve is closed, the action point of the spring force makes the top of the disc close first, so that the valve can maintain the sealing integrity for a longer time.
2. Independent spring structure
The spring with a diameter of DN150 and above enables greater torque to be applied to each valve disc, and the valve disc can be closed independently as the industrial liquid flow changes. Experiments have shown that this effect extends the service life of the valve by 25% and reduces the water hammer by 50%.
Each part of the double disc has its springs which provide independent closing force and experience a relatively small angular deflection of only 140, instead of conventional springs with double brackets with an angle of 350.
Figure 3 The structure of the independent spring
3. Independent disc suspension structure
The independent hinge reduces friction by 66%, which greatly improves the response of the valve. The support sleeve is inserted from the outer hinge so that the upper hinge can be independently supported by the lower sleeve during valve operation. This allows both discs to react quickly and close simultaneously for excellent dynamic performance.
4. The connection with the pipeline
The double plate butterfly check valve and the pipeline can be connected by the wafer, lug wafer, flange and clamp. See Figure 4 for the connection.
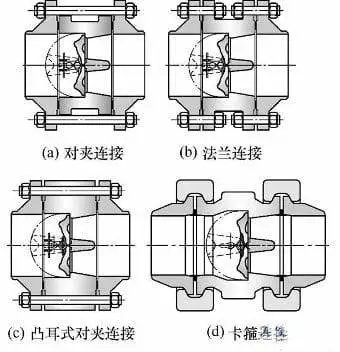
(a) Wafer type (b) Flange ends (c) Lug type (d) Clamp type
Figure 4 The connection between the double plate butterfly check valve and the pipeline
The double plate light structure of the double plate butterfly check valve makes the seat sealing and operation more effective. The long-arm spring of the double plate butterfly check valve enables the disc to open and close without rubbing against the valve seat, and the spring acts independently to close the disc (DN150 and above). The hinge support sleeve of the double plate butterfly check valve reduces friction and minimizes water hammer when stopped by the independent disc with bigger sizes.
Compared with conventional swing check valves, double plate butterfly check valves are generally stronger, lighter, smaller, more efficient, and less expensive. This valve complies with the API 594 standard. For most diameters, the face-to-face size of this valve is only 1/4 of that of conventional valves, and its weight is 15% to 20% of conventional valves, so it is cheaper than swing check valves. It is also easier to install between standard gaskets and pipe flanges. Since it is easy to handle and requires only one set of flange connection bolts, it also saves parts during installation, saving installation costs and daily maintenance costs.
The double plate butterfly check valve also has special structural features, which makes this valve a high-performance non-impact check valve. These features include no-clean opening, independent spring for most valves, and independent disc support systems. Some check valves do not have these features. Double plate butterfly check valve can also be designed with lugs, double flanges and extended valve bodies.
1. Opening and closing processes
The opening and closing process of the double plate butterfly check valve is shown in Figure 2.
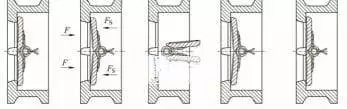
Figure 2 Opening and closing processes of the double plate butterfly check valve
The double-disc structure adopts two spring-loaded discs (half discs), suspended from a central vertical hinge pin. When fluid flows, the disc opens under the resultant force (F) acting on the center of the sealing surface. The acting point of the reacting spring support force (FS) is located outside the center of the disc face, causing the root of the disc to open first. This avoids friction of the sealing surface of the conventional valve when the disc is opened, and eliminates the wear and tear of the components.
When the flow rate slows down, the torsion spring reacts automatically, so that the disc closes and approaches the valve seat of the valve body, reducing the closing stroke distance and time. When the fluid flows backward, the valve disc gradually approaches the valve seat of the valve body, and the dynamic response of the valve is greatly accelerated, which reduces the influence of the water hammer, thereby achieving nonimpact. When the valve is closed, the action point of the spring force makes the top of the disc close first, so that the valve can maintain the sealing integrity for a longer time.
2. Independent spring structure
The spring with a diameter of DN150 and above enables greater torque to be applied to each valve disc, and the valve disc can be closed independently as the industrial liquid flow changes. Experiments have shown that this effect extends the service life of the valve by 25% and reduces the water hammer by 50%.
Each part of the double disc has its springs which provide independent closing force and experience a relatively small angular deflection of only 140, instead of conventional springs with double brackets with an angle of 350.
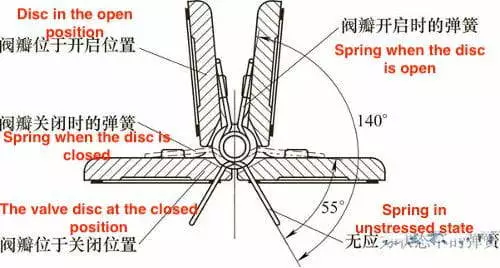
Figure 3 The structure of the independent spring
3. Independent disc suspension structure
The independent hinge reduces friction by 66%, which greatly improves the response of the valve. The support sleeve is inserted from the outer hinge so that the upper hinge can be independently supported by the lower sleeve during valve operation. This allows both discs to react quickly and close simultaneously for excellent dynamic performance.
4. The connection with the pipeline
The double plate butterfly check valve and the pipeline can be connected by the wafer, lug wafer, flange and clamp. See Figure 4 for the connection.
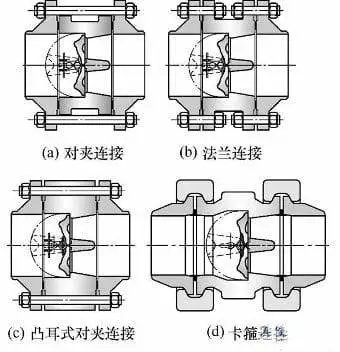
(a) Wafer type (b) Flange ends (c) Lug type (d) Clamp type
Figure 4 The connection between the double plate butterfly check valve and the pipeline
Previous: Selecting Check Valves in Large Seawater Desalination Projects
Next: Reason for Defects in Welding Groove of Valves and Pipelines