Selection of Materials and Components of Plug Valves
Aug 14, 2023
Since the operating conditions are high temperature and high pressure, and the medium is highly corrosive and toxic hydrofluoric acid. To improve the corrosion resistance of the valve and at the same time consider the economic efficiency of the equipment, the plug valve should be made from Ni-Cu alloy as a whole. Ni-Cu alloy is corrosion-resistant in hydrofluoric acid at all concentrations and temperatures, that is, its stability is outstanding, and it is less affected by the flow rate. Therefore, pumps, valves and other equipment and parts under high flow rate conditions use Ni-Cu alloys that are more suitable. In the HF alkylation unit system, the alloy can meet the requirement for design and achieve a relatively reliable labor protection effect. The valve body, bonnet and valve plug of the integral Ni-Cu alloy valve are made from HS-1 grade cast Ni-Cu alloy, and its chemical composition (%) and mechanical properties are shown in Table 5.
The bonnet, metal diaphragm and packing gland are made from Ni-Cu alloy, the gasket flexible graphite, and the sealing diaphragm PTEE or F46.
Table 5 Chemical composition and mechanical properties of HS-1
The bonnet, metal diaphragm and packing gland are made from Ni-Cu alloy, the gasket flexible graphite, and the sealing diaphragm PTEE or F46.
Table 5 Chemical composition and mechanical properties of HS-1
Chemical composition | Ni | Co | Cr | Mo | Fe | C | Si | Mn | W | Cu | Others |
Quality score, % | 67 | - | - | - | 1.4 | 0.15 | - | - | - | 30 | 1.45 |
Tensile strength | Yield strength | Elongation rates | Hardness HBW | ||||||||
600 to 880 | 390 to 840 | 10 to 35 | 160 to 250 |
4. Sealing of plug valves
In the HF alkylation unit, because the liquefied petroleum gas is flammable and explosive, and the catalyst HF is highly corrosive and toxic, the requirements for labor protection are relatively high. Therefore, the requirement for sealing the plug valve is relatively high. To improve the sealing performance, The traditional plug valve has been improved, as shown in Figure 4.
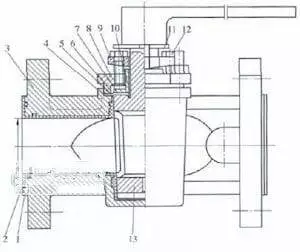
1. Spiral wound gaskets 2. Sealing bushing 3. Valve bodies 4. Gaskets 5. Sealing diaphragms 6. Metal diaphragms 7. Packing sleeves 8. Valve bonnets 9. Adjusting discs 10. Packing 11. Positioning plates 12. Bolts 13. Valve plugs
Figure 4 Structural diagram of plug valves
The sealing mechanism is as follows: a special PFA sealing bushing is pressed into the inside and end of the entire cock cavity, and the inverted trapezoidal groove on the valve body and the cock is well fitted with the sealing sleeve to achieve a good sealing effect. The valve stem and the plug body are of an integral structure, which simplifies the manufacturing process. As shown in Figure 4, the lower part of the valve stem’s sealing device is a flexible graphite gasket, and there is a PTEE or F46 sealing diaphragm on it; the top is covered with a Ni-Cu alloy metal diaphragm. Cu alloy metal diaphragm, PTEE or F46 sealing diaphragm and flexible graphite gasket are pressed well with the valve body to prevent HF from leaking through the valve body. There is also a packing gland on the valve stem, and a circle of flexible graphite packing is installed on the lower part of the gland, which is pressed well by bolts. On the one hand, the packing is squeezed on the valve stem, and on the other hand, the above two diaphragms and gaskets are pressed into the deep groove where the plug connects to the stem to form a reverse lip seal. This kind of seal can play a self-sealing role by means of the pressure inside the valve, which can effectively prevent the leakage of HF. In addition, the flexible graphite filler and gasket in the sealing device can prevent the medium in the valve from leaking into the atmosphere in case of fire. The connection between the valve body and the pipe is also a place where the leakage is likely to occur, so it should also be sealed. The end face is connected to the pipeline with a flange due to the large size of the valve body, and the outer periphery of the sealing bush is sealed with a metal spiral wound gasket, which further strengthens the seal.
Conclusion
1) The seal at the valve stem of this plug valve is safer and more reliable, and the integral bushing in the valve effectively prevents internal leakage and reduces process losses. Compared with ordinary plug valves, this valve has good sealing performance and corrosion resistance, and has fire protection, small opening and closing torque, and can meet the requirements for the production of the alkylation unit.
2) The results of ANSYS analysis show that the main stress concentration part of the valve body is the connection between the valve cylinder and the channel, which provides a reliable basis for the design of the valve and the casting production process. During design, pay attention to reducing the stress concentration here, and the thickness should be appropriately increased to reduce the possibility of failure.
3) The overall bushing inside the valve wastes material. To make the bushing fit better on the inner wall of the valve, it is necessary to process several process grooves inside the valve body, which increases the processing technology.
Previous: Design of Plug Valves in the Refinery Alkylation Unit
Next: Valves Used for the Coal Chemical Industry