Internal Leakages of Ball Valves
Feb 03, 2024
Ball valves are widely used due to their rapid opening and closing, small flow resistance, and good sealing performance. However, internal leakages of ball valves occur frequently due to various reasons such as manufacturing, installation, construction, transportation, operation and maintenance, which pose a threat to the safety production of pipelines. Therefore, studying the principle and treatment measures of internal leakages of valves and proposing a standardized process for internal leakage to reduce the failure rate is of great significance to the safe and stable operation of pipelines.
Internal leakages of ball valves
It was found in statistics on the China-Myanmar natural gas pipeline managed by a company in Guangxi that internal leakage accounts for 84% of the total number of failures of ball valves, as shown in Figure 1, which seriously affects the service life of the valve. The ball valve is composed of a valve body, a ball, a sealing ring, a valve stem and a driving device. It plays the role of cutting off, distributing and changing the flow direction of the medium in natural gas pipelines. According to the structure type of ball valve, ball valves can be divided into two categories: trunnion ball valves and floating ball valves. Trunnion ball valves refer to a ball valve in which the ball is fixed; the valve seat floats under the action of medium pressure, and the sealing ring is well pressed against the ball to ensure sealing. This kind of ball valve has a complex structure and large size but is easy to operate and is suitable for high-pressure and large-diameter pipelines. The ball of the floating ball valve is movable, generating a certain displacement under the action of medium pressure, and well fitting the sealing ring at the outlet end to ensure the sealing. This kind of ball valve has good sealing performance on one side. It is suitable for low-pressure and small-diameter pipelines, but when the pipeline pressure is low and the ball is heavy, the valve sealing effect is poor.
2. Analyzing internal leakages
2.1 Causes of internal leakages of ball valves
Most internal leaks are caused by improper manufacturing, transportation, construction and installation, operation and maintenance.
(1) Manufacturing and transportation: The manufacturer's manufacturing precision is low, resulting in the ball valve not meeting the design requirements in terms of material selection, heat treatment and roughness, causing problems with the quality of the valve; the valve isn’t protected or improperly protected during transportation from the manufacturer to the station, allowing hard particle impurities to enter the inside of the valve, causing damage to the valve.
(2) Construction and installation: Construction was not carried out in strict accordance with the standards. Blind plates were not installed on both sides of the valve during construction, causing rainwater, hard particles, dirt and iron filings to enter the interior of the valve; grease was not injected into the valve seat during installation, causing impurities to enter the back of the valve seat; the temperature was not strictly controlled during welding, which burned the sealing ring and sealing surface, causing internal leakages; the welding slag was not removed after installation, causing scratches on the sealing surface; the valve limit was improperly adjusted during installation, causing internal leakages of the valve; during the strength test of the valve after installation, the pressure was higher than the specified pressure, causing damage to the valve seat.
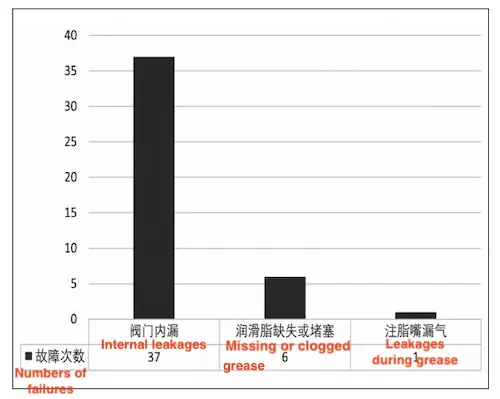
Figure 1 Statistics of failures of ball valves in the China-Myanmar natural gas pipeline managed by a company in Guangxi
(3) Operation and maintenance: The valve user fails to perform maintenance in time due to maintenance costs and other issues; valves that have not been operated for more than 6 months may cause the valve seat and ball to stuck, and damage the sealing surface when the valve is opened and closed; incorrect limit setting of the actuator and corrosion of the limit may cause the valve to not to be opened or closed well. Generally, an angle of 2 to 3 may cause internal leakages of the valve.
2.2 Treatment of internal leakages of valves
Internal leakages of the valve can be treated by adjusting the valve limit, injecting grease into the valve, injecting sealing grease, grinding and repairing, as shown in Figure 2.
2.2.1 Incorrect valve limits
Loose valve limit bolts may cause the valve to not be closed well, causing internal leakage of the valve. This situation is more common in the early stages of installation and construction of valves and can be dealt with by readjusting the limit. During pigging on valves that have been operating stably for a long time, the pigging ball may impact the valve due to improper valve opening angle, which may also cause the valve limit bolts to loosen.
2.2.2 Impurities on the sealing surface
Deterioration of grease, corrosion of sealing surfaces, or a small part of impurities in natural gas adhering to the sealing surface may cause internal leakages of the valve. This situation is more common in ball valves that have not been opened or closed for a long time. This type of failure is diagnosed when the valve chamber pressure cannot be reduced to 0 during the valve chamber emptying process. This fault can be solved by injecting cleaning fluid and soaking it for 1 to 6 hours to soften and completely remove the deteriorated grease on the valve seat and spherical surface, and then inject 80# grease for treatment. In addition to strengthening the sealing effect, grease can also form a protective film on the sealing surface to reduce wear on the sealing surface. If it still cannot be handled, after thorough cleaning, inject type 933 grease with higher consistency. However, type 933 sealing grease will affect the soft seal of the valve seat to a certain extent, so it needs to be used with caution.
2.2.3 Damage to sealing surfaces
During the operation of the ball valve, due to the low processing capacity of the filter separator and accidental falling objects during equipment maintenance, untreated small particle impurities, welding slag and iron wire in the natural gas cause permanent scratches on the valve sealing surface. The method for determining this type of failure is that during the valve cavity emptying process, the valve cavity pressure drops significantly; when the amount of leakage of the sealing surface is equal to that relieved by the valve cavity, the pressure no longer continues to decrease. This fault can be solved by injecting a full volume of standard sealing grease and then conducting a cutoff and drainage test. If the problem still cannot be solved after injecting sealing grease twice, inject half the volume of severe leaking sealing grease (5050#) for a temporary solution. This measure buys some time for the procurement and replacement of sealing parts and the repair of internal leakages of the valve.
2.2.4 Failures of valve bodies
In the emptying process of the valve cavity, if the valve cavity pressure does not change, it means that the leakage’s amount of the sealing surface is approximately equal to the discharge’s amount of the valve cavity. This fault needs to be returned to the factory for repair or internal leakage repair.
Internal leakages of ball valves
It was found in statistics on the China-Myanmar natural gas pipeline managed by a company in Guangxi that internal leakage accounts for 84% of the total number of failures of ball valves, as shown in Figure 1, which seriously affects the service life of the valve. The ball valve is composed of a valve body, a ball, a sealing ring, a valve stem and a driving device. It plays the role of cutting off, distributing and changing the flow direction of the medium in natural gas pipelines. According to the structure type of ball valve, ball valves can be divided into two categories: trunnion ball valves and floating ball valves. Trunnion ball valves refer to a ball valve in which the ball is fixed; the valve seat floats under the action of medium pressure, and the sealing ring is well pressed against the ball to ensure sealing. This kind of ball valve has a complex structure and large size but is easy to operate and is suitable for high-pressure and large-diameter pipelines. The ball of the floating ball valve is movable, generating a certain displacement under the action of medium pressure, and well fitting the sealing ring at the outlet end to ensure the sealing. This kind of ball valve has good sealing performance on one side. It is suitable for low-pressure and small-diameter pipelines, but when the pipeline pressure is low and the ball is heavy, the valve sealing effect is poor.
2. Analyzing internal leakages
2.1 Causes of internal leakages of ball valves
Most internal leaks are caused by improper manufacturing, transportation, construction and installation, operation and maintenance.
(1) Manufacturing and transportation: The manufacturer's manufacturing precision is low, resulting in the ball valve not meeting the design requirements in terms of material selection, heat treatment and roughness, causing problems with the quality of the valve; the valve isn’t protected or improperly protected during transportation from the manufacturer to the station, allowing hard particle impurities to enter the inside of the valve, causing damage to the valve.
(2) Construction and installation: Construction was not carried out in strict accordance with the standards. Blind plates were not installed on both sides of the valve during construction, causing rainwater, hard particles, dirt and iron filings to enter the interior of the valve; grease was not injected into the valve seat during installation, causing impurities to enter the back of the valve seat; the temperature was not strictly controlled during welding, which burned the sealing ring and sealing surface, causing internal leakages; the welding slag was not removed after installation, causing scratches on the sealing surface; the valve limit was improperly adjusted during installation, causing internal leakages of the valve; during the strength test of the valve after installation, the pressure was higher than the specified pressure, causing damage to the valve seat.
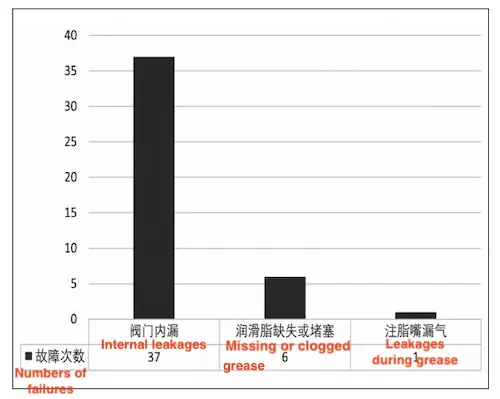
Figure 1 Statistics of failures of ball valves in the China-Myanmar natural gas pipeline managed by a company in Guangxi
(3) Operation and maintenance: The valve user fails to perform maintenance in time due to maintenance costs and other issues; valves that have not been operated for more than 6 months may cause the valve seat and ball to stuck, and damage the sealing surface when the valve is opened and closed; incorrect limit setting of the actuator and corrosion of the limit may cause the valve to not to be opened or closed well. Generally, an angle of 2 to 3 may cause internal leakages of the valve.
2.2 Treatment of internal leakages of valves
Internal leakages of the valve can be treated by adjusting the valve limit, injecting grease into the valve, injecting sealing grease, grinding and repairing, as shown in Figure 2.
2.2.1 Incorrect valve limits
Loose valve limit bolts may cause the valve to not be closed well, causing internal leakage of the valve. This situation is more common in the early stages of installation and construction of valves and can be dealt with by readjusting the limit. During pigging on valves that have been operating stably for a long time, the pigging ball may impact the valve due to improper valve opening angle, which may also cause the valve limit bolts to loosen.
2.2.2 Impurities on the sealing surface
Deterioration of grease, corrosion of sealing surfaces, or a small part of impurities in natural gas adhering to the sealing surface may cause internal leakages of the valve. This situation is more common in ball valves that have not been opened or closed for a long time. This type of failure is diagnosed when the valve chamber pressure cannot be reduced to 0 during the valve chamber emptying process. This fault can be solved by injecting cleaning fluid and soaking it for 1 to 6 hours to soften and completely remove the deteriorated grease on the valve seat and spherical surface, and then inject 80# grease for treatment. In addition to strengthening the sealing effect, grease can also form a protective film on the sealing surface to reduce wear on the sealing surface. If it still cannot be handled, after thorough cleaning, inject type 933 grease with higher consistency. However, type 933 sealing grease will affect the soft seal of the valve seat to a certain extent, so it needs to be used with caution.
2.2.3 Damage to sealing surfaces
During the operation of the ball valve, due to the low processing capacity of the filter separator and accidental falling objects during equipment maintenance, untreated small particle impurities, welding slag and iron wire in the natural gas cause permanent scratches on the valve sealing surface. The method for determining this type of failure is that during the valve cavity emptying process, the valve cavity pressure drops significantly; when the amount of leakage of the sealing surface is equal to that relieved by the valve cavity, the pressure no longer continues to decrease. This fault can be solved by injecting a full volume of standard sealing grease and then conducting a cutoff and drainage test. If the problem still cannot be solved after injecting sealing grease twice, inject half the volume of severe leaking sealing grease (5050#) for a temporary solution. This measure buys some time for the procurement and replacement of sealing parts and the repair of internal leakages of the valve.
2.2.4 Failures of valve bodies
In the emptying process of the valve cavity, if the valve cavity pressure does not change, it means that the leakage’s amount of the sealing surface is approximately equal to the discharge’s amount of the valve cavity. This fault needs to be returned to the factory for repair or internal leakage repair.
Previous: Applications of Valve Management Systems in Water Supply Pipes
Next: Measures for Internal Leakage of Ball Valves