Design Analysis of High Temperature Valves
May 18, 2022
At present, with the continuous progress and development of society, China has begun to use various professional technologies to design the identification function of high-temperature valves. For this reason, it is necessary to report and practice the big data according to the corresponding data. Because there are still many defects in the design and management of high-temperature valves in China, it is necessary to improve some of the problems in multiple ways according to the existing actual situation, so as to promote the sustainable progress and development of the technical design of this kind of high-temperature valve designing structure.
Material selection of high-temperature valves for internal combustion engines
1. Material selection of valves
In order to further ensure that the high-temperature valves of internal combustion engines can be affected by various temperatures during structural management, and the physical properties and structural properties will not change, the valve materials must be selected according to the actual situation on the spot and the firing technology of the valves. Generally speaking, the commonly used valve materials are carbon steel, stainless steel and high-temperature resistant alloy steel. In order to ensure the basic requirements of the internal setting of the valve, it is necessary to meet the requirements of controlling its scouring force and corrosivity. When selecting the internal material of the valve, the material's thermal expansion and cold contraction must be regarded as essential elements for the valve selection. At the same time, the basic components of the valve should be managed according to the high temperature of the material, so that the main material inside the valve can be made of stainless steel and other factors. Various aluminum alloys can be surfacing on the surface. Ceramic surfacing is adopted to ensure the wear resistance and corrosion resistance of the valve so that it can run normally at a high temperature of 800 degrees Celsius.
2. Analysis of the design structure of high-temperature valves for the internal combustion engine
In the process of shell design, it is necessary to fully consider the possible maximum pressure value of the actual application situation. At the same time, it should be designed to control the rated value of shell pressure resistance, so as to ensure that it can have enough pressure resistance and minimize the adverse effects of corrosion and erosion. In addition, it is necessary to analyze the sealing structure effectively, and design it as a multi-element integrated sealing gasket for pressure control, so that it can produce compressibility and fill the tiny cracks on its surface. This kind of mandatory sealing management is very common in the design of valves with medium temperature and small diameter, which can make the bolts tighten before boosting so that the tightness of the valve cover and the elastic device increases. The valve cover moves upwards, so as to contain the bolts and improve the unloading efficiency. Not only that, but when the valve is sealed, it is necessary to ensure its influence on the pressure. The early warning sealing specific pressure and medium pressure is used to make the enterprise have a joint influence. If the temperature between them keeps rising, the tightness of its work will also increase, which may have a greater impact on the subsequent valves' design structure. For the design and management of high-temperature valves, it is necessary to carry out technical reform and innovation according to the actual situation, improving the basic material settings according to the actual needs, and enhancing the operation and management of its automatic function system.
3. Related connection methods of high-temperature bolts
When bolting high-temperature valves, it is necessary to consider the changes in mechanical properties of the connected objects at high temperatures, so that the stress management can be consistent with the actual situation. Not only that, in order to further avoid the failure of the thread at high temperature, it is necessary to select the material scientifically, so that the thread can be designed into a coarse thread state. The middle gap stitching can be increased within a reasonable range, so as to ensure that the residual early warning force is higher than the required value and to determine the stability and professionalism of the connection. At the same time, according to the actual situation, it is necessary to keep a proper gap between the sealing seat on the valve stem and ensure that the latter is larger than the former in terms of material expansion and contraction, otherwise, there will be problems such as wear and tear.
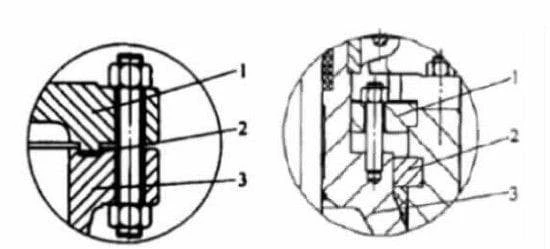
1- valve cover; 2- gasket; 3- valve body
1- support ring; 2- four open loops; 3- bonnet
Key Technology of Valve Design for Internal Combustion Engines
1. Analysis of thermal expansion variables
In the design and management of high-temperature valves of internal combustion engines, the thermal expansion factors of materials and the different factors of parts bearing capacity must be taken into account. In the design and management of high-temperature valves, the temperature of the chip inside the valve is quickly consistent with the temperature of the pipeline fluid, and the high-temperature fluid must be introduced into the valve with a lower temperature. The valve stem with a small cross-sectional area can fully utilize the chip for heat dissipation, so as to ensure that its heat dissipation conditions and the internal temperature of the valve are within a certain reasonable control range. Although they are heated together, the expansion amount is inconsistent. Therefore, in order to further ensure the increase of the working gap between parts, it is necessary to ensure that the parts are prevented from sticking and scratching under the condition of a high-temperature medium, to minimize the trauma caused by the temperature of the parts, and to keep enough content of the gap while increasing. It should be determined and managed according to the system stress of the high-temperature coefficient of the material and the actual use temperature, and the site should be controlled according to the actual situation.
2. Analysis of heat exchange variables
In the continuous development of society, it is necessary to learn from the changes in heat exchange variables to conduct a reasonable control analysis of the interaction between components, so that the original sealing effect loses its implied value. Therefore, in the management, it must be properly treated in multiple ways, so that the joint between the two components can be seam-welded to ensure its original sealing effect. In addition, it is necessary to enhance the collision between parts of the valve body according to the large-diameter valve, to reduce people's visual fatigue, and to enhance the sealing effect between parts. Therefore, when designing, it is necessary to select the structure and evaluate the effect according to the closed elasticity of the heat exchange variable, and reduce the influence of hot film on the high-temperature valve and the damage degree of parts according to the existing actual situation, so as to maximize the service life of the high-temperature valve and further lay the foundation for the subsequent valves variable design. In addition, in order to further realize the hardening treatment inside the high-temperature valve, it is necessary to confirm the thickness of the surfacing layer, judge the thickness of the surfacing layer by some useful experiments, and select a suitable thickness to isolate the external high-temperature design, so as to reduce the influence of the external high temperature on the internal materials and ensure the service life of the internal valve.
3. When managing the design of wear-resistant coating inside the internal combustion engine valve, it is necessary to ensure the high-temperature resistance and corrosion resistance according to the actual situation of its design. The wear-resistant coating inside the valve must be carried out under the condition of high-temperature work, and the selection skill of wear-resistant coating should be used to fully harden and manage it. In order to meet this requirement, it is necessary to choose a high-speed spraying process and spray a layer of corresponding high-temperature resistant coating inside the high-temperature ball valve body to ensure its normal operation at various temperatures. In addition, it is necessary to coat a layer of stone-resistant coating to ensure that the valve can meet the application requirements at high temperatures according to the existing actual situation so that the coating will not fall off when heated at high temperatures. Not only that, the valve stem sealing design structure of the high-temperature ball valve must adopt the existing scientific and technological levels to analyze it in multiple ways. The conical container is an ink ring combined packing so that the upper and lower layers are made of flexible graphite braided additives, and the middle three layers are made of flexible graphite rings with low density to contact the inclined plane so that the valve stem can achieve a better sealing effect. In addition, if there is a certain degree of difference between materials, it may cause external abrasion due to the influence of its external environment, which will reduce the vibration impact and meta abrasion caused by large particles of the valve seat and valve core in the system management. To this, in the process of its operation, different materials of the seal must be selected according to the actual situation to ensure that the hardness matching value of the seal is in a reasonable range.
To sum up, at present, the application range of key technologies of high-temperature valves is becoming wider and wider, and the requirements of the public are also increasing. During this period, it is still necessary to control, analyze and deal with it according to the actual situation of the site, gradually improve its construction management requirements, and make preparations for the subsequent construction. Therefore, it is necessary to study and control the technical design of high-temperature valves, and to improve their service life and efficiency by selecting materials and controlling the temperature of hardened valves.
Material selection of high-temperature valves for internal combustion engines
1. Material selection of valves
In order to further ensure that the high-temperature valves of internal combustion engines can be affected by various temperatures during structural management, and the physical properties and structural properties will not change, the valve materials must be selected according to the actual situation on the spot and the firing technology of the valves. Generally speaking, the commonly used valve materials are carbon steel, stainless steel and high-temperature resistant alloy steel. In order to ensure the basic requirements of the internal setting of the valve, it is necessary to meet the requirements of controlling its scouring force and corrosivity. When selecting the internal material of the valve, the material's thermal expansion and cold contraction must be regarded as essential elements for the valve selection. At the same time, the basic components of the valve should be managed according to the high temperature of the material, so that the main material inside the valve can be made of stainless steel and other factors. Various aluminum alloys can be surfacing on the surface. Ceramic surfacing is adopted to ensure the wear resistance and corrosion resistance of the valve so that it can run normally at a high temperature of 800 degrees Celsius.
2. Analysis of the design structure of high-temperature valves for the internal combustion engine
In the process of shell design, it is necessary to fully consider the possible maximum pressure value of the actual application situation. At the same time, it should be designed to control the rated value of shell pressure resistance, so as to ensure that it can have enough pressure resistance and minimize the adverse effects of corrosion and erosion. In addition, it is necessary to analyze the sealing structure effectively, and design it as a multi-element integrated sealing gasket for pressure control, so that it can produce compressibility and fill the tiny cracks on its surface. This kind of mandatory sealing management is very common in the design of valves with medium temperature and small diameter, which can make the bolts tighten before boosting so that the tightness of the valve cover and the elastic device increases. The valve cover moves upwards, so as to contain the bolts and improve the unloading efficiency. Not only that, but when the valve is sealed, it is necessary to ensure its influence on the pressure. The early warning sealing specific pressure and medium pressure is used to make the enterprise have a joint influence. If the temperature between them keeps rising, the tightness of its work will also increase, which may have a greater impact on the subsequent valves' design structure. For the design and management of high-temperature valves, it is necessary to carry out technical reform and innovation according to the actual situation, improving the basic material settings according to the actual needs, and enhancing the operation and management of its automatic function system.
3. Related connection methods of high-temperature bolts
When bolting high-temperature valves, it is necessary to consider the changes in mechanical properties of the connected objects at high temperatures, so that the stress management can be consistent with the actual situation. Not only that, in order to further avoid the failure of the thread at high temperature, it is necessary to select the material scientifically, so that the thread can be designed into a coarse thread state. The middle gap stitching can be increased within a reasonable range, so as to ensure that the residual early warning force is higher than the required value and to determine the stability and professionalism of the connection. At the same time, according to the actual situation, it is necessary to keep a proper gap between the sealing seat on the valve stem and ensure that the latter is larger than the former in terms of material expansion and contraction, otherwise, there will be problems such as wear and tear.
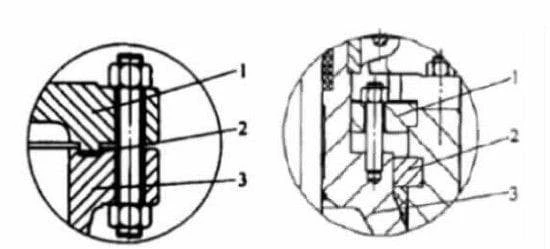
1- valve cover; 2- gasket; 3- valve body
1- support ring; 2- four open loops; 3- bonnet
Key Technology of Valve Design for Internal Combustion Engines
1. Analysis of thermal expansion variables
In the design and management of high-temperature valves of internal combustion engines, the thermal expansion factors of materials and the different factors of parts bearing capacity must be taken into account. In the design and management of high-temperature valves, the temperature of the chip inside the valve is quickly consistent with the temperature of the pipeline fluid, and the high-temperature fluid must be introduced into the valve with a lower temperature. The valve stem with a small cross-sectional area can fully utilize the chip for heat dissipation, so as to ensure that its heat dissipation conditions and the internal temperature of the valve are within a certain reasonable control range. Although they are heated together, the expansion amount is inconsistent. Therefore, in order to further ensure the increase of the working gap between parts, it is necessary to ensure that the parts are prevented from sticking and scratching under the condition of a high-temperature medium, to minimize the trauma caused by the temperature of the parts, and to keep enough content of the gap while increasing. It should be determined and managed according to the system stress of the high-temperature coefficient of the material and the actual use temperature, and the site should be controlled according to the actual situation.
2. Analysis of heat exchange variables
In the continuous development of society, it is necessary to learn from the changes in heat exchange variables to conduct a reasonable control analysis of the interaction between components, so that the original sealing effect loses its implied value. Therefore, in the management, it must be properly treated in multiple ways, so that the joint between the two components can be seam-welded to ensure its original sealing effect. In addition, it is necessary to enhance the collision between parts of the valve body according to the large-diameter valve, to reduce people's visual fatigue, and to enhance the sealing effect between parts. Therefore, when designing, it is necessary to select the structure and evaluate the effect according to the closed elasticity of the heat exchange variable, and reduce the influence of hot film on the high-temperature valve and the damage degree of parts according to the existing actual situation, so as to maximize the service life of the high-temperature valve and further lay the foundation for the subsequent valves variable design. In addition, in order to further realize the hardening treatment inside the high-temperature valve, it is necessary to confirm the thickness of the surfacing layer, judge the thickness of the surfacing layer by some useful experiments, and select a suitable thickness to isolate the external high-temperature design, so as to reduce the influence of the external high temperature on the internal materials and ensure the service life of the internal valve.
3. When managing the design of wear-resistant coating inside the internal combustion engine valve, it is necessary to ensure the high-temperature resistance and corrosion resistance according to the actual situation of its design. The wear-resistant coating inside the valve must be carried out under the condition of high-temperature work, and the selection skill of wear-resistant coating should be used to fully harden and manage it. In order to meet this requirement, it is necessary to choose a high-speed spraying process and spray a layer of corresponding high-temperature resistant coating inside the high-temperature ball valve body to ensure its normal operation at various temperatures. In addition, it is necessary to coat a layer of stone-resistant coating to ensure that the valve can meet the application requirements at high temperatures according to the existing actual situation so that the coating will not fall off when heated at high temperatures. Not only that, the valve stem sealing design structure of the high-temperature ball valve must adopt the existing scientific and technological levels to analyze it in multiple ways. The conical container is an ink ring combined packing so that the upper and lower layers are made of flexible graphite braided additives, and the middle three layers are made of flexible graphite rings with low density to contact the inclined plane so that the valve stem can achieve a better sealing effect. In addition, if there is a certain degree of difference between materials, it may cause external abrasion due to the influence of its external environment, which will reduce the vibration impact and meta abrasion caused by large particles of the valve seat and valve core in the system management. To this, in the process of its operation, different materials of the seal must be selected according to the actual situation to ensure that the hardness matching value of the seal is in a reasonable range.
To sum up, at present, the application range of key technologies of high-temperature valves is becoming wider and wider, and the requirements of the public are also increasing. During this period, it is still necessary to control, analyze and deal with it according to the actual situation of the site, gradually improve its construction management requirements, and make preparations for the subsequent construction. Therefore, it is necessary to study and control the technical design of high-temperature valves, and to improve their service life and efficiency by selecting materials and controlling the temperature of hardened valves.
Previous: How to Prolong the Service Life of Ball Valves?
Next: The Difference between Bellows Globe Valves and Common Ones