Are Safety Valves Safe and Reliable Enough?
Apr 20, 2022
The answer is yes. The technical development of key equipment is faster than we thought. Safety valves have been widely used in various devices in factories to protect the safety of equipment and personnel. As the last line of defense for safe production, safety valves must provide effective overpressure protection when overpressure accidents occur and after all other emergency operations fail. Over the past century, the design of safety valves has only changed slightly, so the digital transformation of safety valves is easy to realize.
Usually, the safety valve is a purely mechanical device, which does not rely on external force, with no additional power supply and air source, but only depends on the force of the system medium itself, and does not go up to the DCS system, as shown in Figure 1. Therefore, it is difficult for factory operators and managers to know the working state of safety valves in real time and accurately.
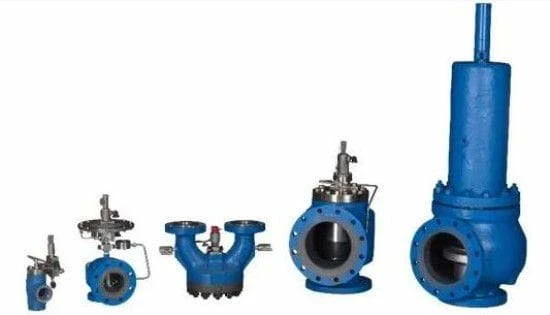
Figure 1: Safety valves are usually not connected to the control system and safety monitoring system of the factory, which brings great challenges to the operation of the factory.
Because of the special and important position of safety valves in factories and the lack of means of condition monitoring, many safety challenges have been brought to the operation of plant devices. The digitalization of safety valves is helpful to solve the safety challenges in the use of safety valves.
The digitalization of safety valves can at least start from two aspects: leakage monitoring and equipment information management, which not only realizes digitalization but also improves the safety and reliability of the safety valve itself.
Leakage Monitoring of Safety Valves
The monitoring of the safety valve's service status includes the monitoring of opening and closing and leakage status, which can record and feedback on the safety valve's running status information the first time.
Impact of Safety Valve Opening or Leakage on Safety, Reliability, Cost and Emission
According to Emerson's research, a large number of overpressure conditions have occurred but have not been found and recorded, and the leakage of safety valves may be less likely to be found than the overpressure relief of safety valves. A better understanding of the causes of the overpressure relief or leakage of these safety valves will improve the profitability and production reliability of the factory, reducing the medium discharge and improving the process safety.
Security
Overpressure relief is an attempted safety accident, but the lower its frequency is, the more effective our operation control will be.
The potential problem is that the frequency of overpressure relief of safety valves is higher than we thought, and it is usually undetected and unreported. If the factory can provide overpressure relief records, it will provide materials and a basis for cause failure analysis and corresponding training, and many problems can be avoided.
Overpressure relief of the safety valve is not a normal working condition, so it should be recorded for further cause analysis and investigation. If the safety valve operates frequently, it may be a process flow problem that deserves more attention.
Reliability
The opening or closing of the safety valve directly or indirectly affects the normal operation of the process flow. If overpressure occurs frequently, not only the sealing surface of the safety valve will be affected, but also the adjacent mechanical equipment, such as the upstream and downstream shut-off valves, and the medium released by overpressure will also affect the smooth operation of the processing unit.
Part of the safety valve began to leak when the operating pressure reached 50% of the set pressure. However, on-site operators didn't notice that a large number of safety valves leaked at the site. The key point was that everyone didn't know when and why the safety valves began to leak.
The most common cause of safety valves leakage is the damage to the valve flap or nozzle after overpressure relief. It may be that the safety valve is not seated correctly. Debris may damage the sealing surface of the valve flap or nozzle, or the valve may flutter when seated.
If the safety valve is not monitored, it is difficult for the staff to know what happened during the overpressure relief.
Cost
If the operating pressure of the system is below the sealing pressure of the safety valve, the safety valve should not leak. However, after analyzing 10,000 safety valve service records of a top refining and chemical integration company, a surprising fact was found.
Before the safety valve is put into use, it needs to be checked to ensure the accuracy of its take-off pressure. The analysis shows that during calibration, 20% of the safety valves will leak when the pressure in front of the valve is lower than 50% of the set pressure, and 8% of them will leak so badly that the test bench cannot provide enough flow to make the safety valves operate.
Even if the leakage rate of a safety valve is only 0.1% of the rated discharge capacity, its leakage in one year is equivalent to 6 hours when the valve is fully opened. When the safety valve is fully opened, the medium released can reach hundreds of tons. Emerson's research shows that a 10-million-ton/year refinery loses more than 10 million yuan in products and energy every year.
Discharge
The discharge and leakage of pollutants (as shown in Figure 2) may lead to fines, lawsuits or extra work to identify the source of discharge and report each leakage. If the concentration and pressure of the medium are high, a small leakage may also lead to a large amount of medium leakage.
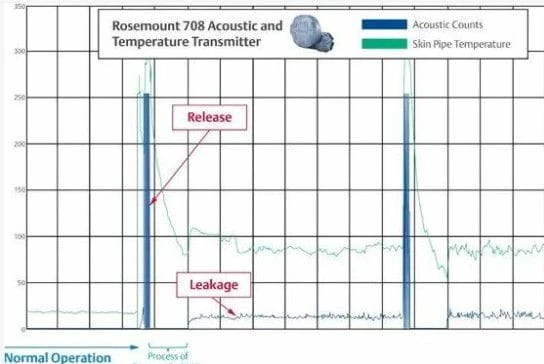
Figure 2: This figure shows a typical leakage accident. After the first discharge, the safety valve was not completely closed. The blue line in the figure shows that the leakage persists, and this leakage is detected by the safety valve monitoring shown in the green line.
The leakage of the safety valve may lead to the compliance of the non-methane total hydrocarbon limit in the factory area and the factory boundary, and may also hinder the company's commitment to achieving ESG goals.
Problems Solving
Through digital transformation technology, continuous monitoring of safety valves operation can be realized. When the valve takes off, the system will give an alarm to the operators and record the time and duration of each overpressure release; It can also tell whether the valve leaks, tremors or frequency jumps. With this real-time information, it is possible to correlate the opening of safety valves with operation data.
Overpressure relief can be associated with historical records and maintenance data. The factory can conduct deeper and more accurate fault analysis not only for valves but also for processes. Maintenance personnel can use data analysis to improve diagnosis and remotely connect with valve experts to help with troubleshooting problems in real-time. Digital transformation can also develop new operating procedures and safety procedures to avoid the recurrence of overpressure conditions. All of the above needs to start with the establishment of monitoring.
There are three main ways to monitor the opening leakage of safety valves. One way is to detect the displacement of the valve stem. This way we can use wireless or wired position transmitters, or limit switches. This way is suitable for spring-type safety valves, but can't monitor the leakage of safety valves well. The second one is realized by monitoring the pressure difference between the upper chamber of the main valve of the pilot valve and the inlet of the safety valve. The corresponding products are wireless or wired differential pressure transmitters, which are suitable for the pilot safety valve but also can't monitor the leakage of the safety valve well. The third one is realized by monitoring the ultrasonic wave of the outlet pipeline when the safety valve discharges or leaks. The corresponding product is the wireless acoustic transmitter, which is suitable for all types of safety valves and can monitor the opening and closing of safety valves well.
For example, we apply the safety valve with its outlet connected to the torch. Many safety valves for non-ordinary gas or steam on site are connected to the torch, including safety valves for non-methane hydrocarbons and toxic and harmful media. When we find that the torch is abnormal, there is usually a problem with the safety valve connected to it, or the safety valve is opened, or the safety valve leaks. At this time, we need to conduct an investigation to locate the safety valve and solve the problem in time. Is there a problem with the safety valve A or the safety valve B? In the past, the safety valve with the problem was found by manual inspection. It is fine that the safety valve is opened. We can also locate it by the sound of the safety valve during discharge. If it is a leakage problem, it will be difficult to schedule the problem. Or we can't find the source of the problem at all, because, after a period of time, the safety valve has been closed, or the leakage no longer exists, so we can't provide a good analysis basis for the operation. Or we found the location of the problem safety valve, but the discharge or leakage of the safety valve has occurred for a long time, which is not only the economic loss caused by the medium loss but more importantly, the potential safety hazard can not be eliminated in time. The wireless sound transmitter is usually installed in the outlet pipeline of the safety valve, and it is installed in a snap type. The principle is that the ultrasonic wave is assisted by temperature, and the wireless sound transmitter transmits the monitoring information to the upper computer through the wireless gateway. After installing the safety valve monitoring equipment, we can get accurate information the first time, and then take corresponding measures the first time.
Monitoring Equipment of Safety Valves
Wireless sound wave transmitters, as shown in Figure 3, can be directly installed on pipelines near process valves, spring-loaded safety valves, pilot-operated safety valves, steam traps and other common fluid control equipment.
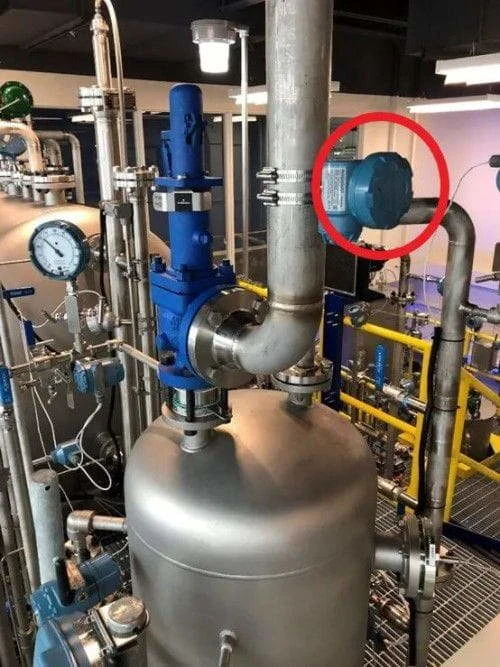
Figure 3: A wireless sound wave transmitter (the blue device at the top right of the photo) is installed on the outlet pipeline of the safety valve, and the vibration caused by any leakage or opening of the safety valve is fed back to the control system through the wireless HART protocol.
The wireless acoustic transmitter can sense the vibration in the pipeline because of the turbulence and vibration in the process of fluid flow. The wireless acoustic transmitter collects the ultrasonic frequencies when vibration occurs, because these frequencies are easy to identify, and will not be affected even in an environment with serious environmental noise.
According to the recorded duration of overpressure relief and the calculated value of unit relief volume of safety valves, the total relief volume of each overpressure can be calculated approximately.
Largely Saving Cost
It is not uncommon for safety valves with the same problems to be put into use again. Real-time monitoring of safety valves provides data for finding out the root cause of the failure. Our safety valve monitoring solution can save tens of millions of yuan in medium loss costs for large refineries.
In addition, there are cost savings from patrol inspection. This solution also eliminates the previous manual inspection in dangerous areas and improves the health and safety of operators. In the past, we learned the working state of safety valves by manual inspection, but manual inspection is facing more and more challenges. First of all, we need to equip the corresponding patrol personnel. As the young people's willingness to work on the front line is getting lower and lower, and the labor cost is constantly increasing, and as the project volume increases, the factory area is getting larger and larger, we need to equip more patrol personnel to cover a larger area of the factory area, which makes the manual patrol to monitor the working state of the safety valve a challenge. There will inevitably be some deviations and information omissions in manual inspection, and there will be inspection efficiency problems in large-scale factory areas. Because the safety valve is installed at a high position. For example, the height of the separation tower exceeds 100m at the highest, which makes the inspection efficiency low, and it is also detrimental to the safety of inspection personnel. At the same time, manual inspection is greatly affected by the weather, and there is no way to conduct an inspection in the season of heavy rain and strong wind or typhoon along the coast; The high temperature, corrosion, toxic and harmful gas environment on site is not suitable for manual inspection.
Another big disadvantage of manual inspection is the delay of time, which can't find the problems the first time. Therefore, there will be a time lag, cost and security challenges in the way of manual inspection. With the online monitoring equipment of safety valves, we can see the problems in the control system the first time, and directly and accurately locate the safety valves with problems, and take timely measures. The open leakage monitoring of safety valves can not only monitor the safety valves provided by us but also provide monitoring services for safety valves of other brands on site.
Usually, the safety valve is a purely mechanical device, which does not rely on external force, with no additional power supply and air source, but only depends on the force of the system medium itself, and does not go up to the DCS system, as shown in Figure 1. Therefore, it is difficult for factory operators and managers to know the working state of safety valves in real time and accurately.
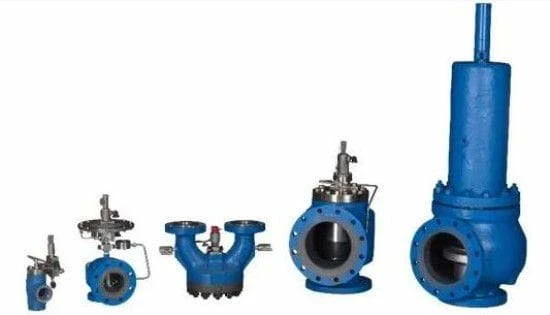
Figure 1: Safety valves are usually not connected to the control system and safety monitoring system of the factory, which brings great challenges to the operation of the factory.
Because of the special and important position of safety valves in factories and the lack of means of condition monitoring, many safety challenges have been brought to the operation of plant devices. The digitalization of safety valves is helpful to solve the safety challenges in the use of safety valves.
The digitalization of safety valves can at least start from two aspects: leakage monitoring and equipment information management, which not only realizes digitalization but also improves the safety and reliability of the safety valve itself.
Leakage Monitoring of Safety Valves
The monitoring of the safety valve's service status includes the monitoring of opening and closing and leakage status, which can record and feedback on the safety valve's running status information the first time.
Impact of Safety Valve Opening or Leakage on Safety, Reliability, Cost and Emission
According to Emerson's research, a large number of overpressure conditions have occurred but have not been found and recorded, and the leakage of safety valves may be less likely to be found than the overpressure relief of safety valves. A better understanding of the causes of the overpressure relief or leakage of these safety valves will improve the profitability and production reliability of the factory, reducing the medium discharge and improving the process safety.
Security
Overpressure relief is an attempted safety accident, but the lower its frequency is, the more effective our operation control will be.
The potential problem is that the frequency of overpressure relief of safety valves is higher than we thought, and it is usually undetected and unreported. If the factory can provide overpressure relief records, it will provide materials and a basis for cause failure analysis and corresponding training, and many problems can be avoided.
Overpressure relief of the safety valve is not a normal working condition, so it should be recorded for further cause analysis and investigation. If the safety valve operates frequently, it may be a process flow problem that deserves more attention.
Reliability
The opening or closing of the safety valve directly or indirectly affects the normal operation of the process flow. If overpressure occurs frequently, not only the sealing surface of the safety valve will be affected, but also the adjacent mechanical equipment, such as the upstream and downstream shut-off valves, and the medium released by overpressure will also affect the smooth operation of the processing unit.
Part of the safety valve began to leak when the operating pressure reached 50% of the set pressure. However, on-site operators didn't notice that a large number of safety valves leaked at the site. The key point was that everyone didn't know when and why the safety valves began to leak.
The most common cause of safety valves leakage is the damage to the valve flap or nozzle after overpressure relief. It may be that the safety valve is not seated correctly. Debris may damage the sealing surface of the valve flap or nozzle, or the valve may flutter when seated.
If the safety valve is not monitored, it is difficult for the staff to know what happened during the overpressure relief.
Cost
If the operating pressure of the system is below the sealing pressure of the safety valve, the safety valve should not leak. However, after analyzing 10,000 safety valve service records of a top refining and chemical integration company, a surprising fact was found.
Before the safety valve is put into use, it needs to be checked to ensure the accuracy of its take-off pressure. The analysis shows that during calibration, 20% of the safety valves will leak when the pressure in front of the valve is lower than 50% of the set pressure, and 8% of them will leak so badly that the test bench cannot provide enough flow to make the safety valves operate.
Even if the leakage rate of a safety valve is only 0.1% of the rated discharge capacity, its leakage in one year is equivalent to 6 hours when the valve is fully opened. When the safety valve is fully opened, the medium released can reach hundreds of tons. Emerson's research shows that a 10-million-ton/year refinery loses more than 10 million yuan in products and energy every year.
Discharge
The discharge and leakage of pollutants (as shown in Figure 2) may lead to fines, lawsuits or extra work to identify the source of discharge and report each leakage. If the concentration and pressure of the medium are high, a small leakage may also lead to a large amount of medium leakage.
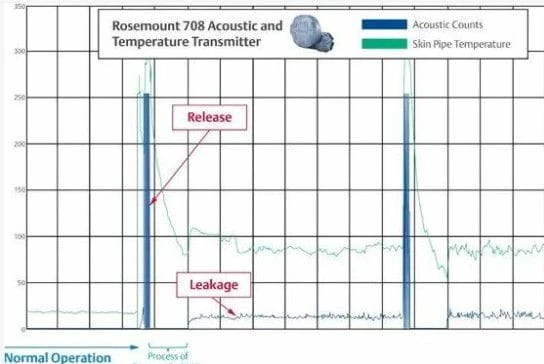
Figure 2: This figure shows a typical leakage accident. After the first discharge, the safety valve was not completely closed. The blue line in the figure shows that the leakage persists, and this leakage is detected by the safety valve monitoring shown in the green line.
The leakage of the safety valve may lead to the compliance of the non-methane total hydrocarbon limit in the factory area and the factory boundary, and may also hinder the company's commitment to achieving ESG goals.
Problems Solving
Through digital transformation technology, continuous monitoring of safety valves operation can be realized. When the valve takes off, the system will give an alarm to the operators and record the time and duration of each overpressure release; It can also tell whether the valve leaks, tremors or frequency jumps. With this real-time information, it is possible to correlate the opening of safety valves with operation data.
Overpressure relief can be associated with historical records and maintenance data. The factory can conduct deeper and more accurate fault analysis not only for valves but also for processes. Maintenance personnel can use data analysis to improve diagnosis and remotely connect with valve experts to help with troubleshooting problems in real-time. Digital transformation can also develop new operating procedures and safety procedures to avoid the recurrence of overpressure conditions. All of the above needs to start with the establishment of monitoring.
There are three main ways to monitor the opening leakage of safety valves. One way is to detect the displacement of the valve stem. This way we can use wireless or wired position transmitters, or limit switches. This way is suitable for spring-type safety valves, but can't monitor the leakage of safety valves well. The second one is realized by monitoring the pressure difference between the upper chamber of the main valve of the pilot valve and the inlet of the safety valve. The corresponding products are wireless or wired differential pressure transmitters, which are suitable for the pilot safety valve but also can't monitor the leakage of the safety valve well. The third one is realized by monitoring the ultrasonic wave of the outlet pipeline when the safety valve discharges or leaks. The corresponding product is the wireless acoustic transmitter, which is suitable for all types of safety valves and can monitor the opening and closing of safety valves well.
For example, we apply the safety valve with its outlet connected to the torch. Many safety valves for non-ordinary gas or steam on site are connected to the torch, including safety valves for non-methane hydrocarbons and toxic and harmful media. When we find that the torch is abnormal, there is usually a problem with the safety valve connected to it, or the safety valve is opened, or the safety valve leaks. At this time, we need to conduct an investigation to locate the safety valve and solve the problem in time. Is there a problem with the safety valve A or the safety valve B? In the past, the safety valve with the problem was found by manual inspection. It is fine that the safety valve is opened. We can also locate it by the sound of the safety valve during discharge. If it is a leakage problem, it will be difficult to schedule the problem. Or we can't find the source of the problem at all, because, after a period of time, the safety valve has been closed, or the leakage no longer exists, so we can't provide a good analysis basis for the operation. Or we found the location of the problem safety valve, but the discharge or leakage of the safety valve has occurred for a long time, which is not only the economic loss caused by the medium loss but more importantly, the potential safety hazard can not be eliminated in time. The wireless sound transmitter is usually installed in the outlet pipeline of the safety valve, and it is installed in a snap type. The principle is that the ultrasonic wave is assisted by temperature, and the wireless sound transmitter transmits the monitoring information to the upper computer through the wireless gateway. After installing the safety valve monitoring equipment, we can get accurate information the first time, and then take corresponding measures the first time.
Monitoring Equipment of Safety Valves
Wireless sound wave transmitters, as shown in Figure 3, can be directly installed on pipelines near process valves, spring-loaded safety valves, pilot-operated safety valves, steam traps and other common fluid control equipment.
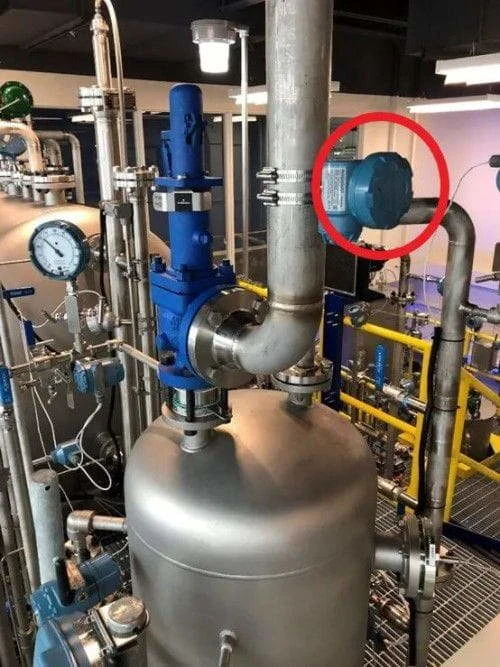
Figure 3: A wireless sound wave transmitter (the blue device at the top right of the photo) is installed on the outlet pipeline of the safety valve, and the vibration caused by any leakage or opening of the safety valve is fed back to the control system through the wireless HART protocol.
The wireless acoustic transmitter can sense the vibration in the pipeline because of the turbulence and vibration in the process of fluid flow. The wireless acoustic transmitter collects the ultrasonic frequencies when vibration occurs, because these frequencies are easy to identify, and will not be affected even in an environment with serious environmental noise.
According to the recorded duration of overpressure relief and the calculated value of unit relief volume of safety valves, the total relief volume of each overpressure can be calculated approximately.
Largely Saving Cost
It is not uncommon for safety valves with the same problems to be put into use again. Real-time monitoring of safety valves provides data for finding out the root cause of the failure. Our safety valve monitoring solution can save tens of millions of yuan in medium loss costs for large refineries.
In addition, there are cost savings from patrol inspection. This solution also eliminates the previous manual inspection in dangerous areas and improves the health and safety of operators. In the past, we learned the working state of safety valves by manual inspection, but manual inspection is facing more and more challenges. First of all, we need to equip the corresponding patrol personnel. As the young people's willingness to work on the front line is getting lower and lower, and the labor cost is constantly increasing, and as the project volume increases, the factory area is getting larger and larger, we need to equip more patrol personnel to cover a larger area of the factory area, which makes the manual patrol to monitor the working state of the safety valve a challenge. There will inevitably be some deviations and information omissions in manual inspection, and there will be inspection efficiency problems in large-scale factory areas. Because the safety valve is installed at a high position. For example, the height of the separation tower exceeds 100m at the highest, which makes the inspection efficiency low, and it is also detrimental to the safety of inspection personnel. At the same time, manual inspection is greatly affected by the weather, and there is no way to conduct an inspection in the season of heavy rain and strong wind or typhoon along the coast; The high temperature, corrosion, toxic and harmful gas environment on site is not suitable for manual inspection.
Another big disadvantage of manual inspection is the delay of time, which can't find the problems the first time. Therefore, there will be a time lag, cost and security challenges in the way of manual inspection. With the online monitoring equipment of safety valves, we can see the problems in the control system the first time, and directly and accurately locate the safety valves with problems, and take timely measures. The open leakage monitoring of safety valves can not only monitor the safety valves provided by us but also provide monitoring services for safety valves of other brands on site.
Previous: Twenty-five Taboos of Valve Installation
Next: How to Prolong the Service Life of Ball Valves?