Anti-corrosion of Valve Surfaces in the Petrochemical Industry
Nov 28, 2023
1. Overview
The petrochemical industry is the pillar industry in China. Most large petrochemical companies have been built in coastal areas in recent years due to raw material transportation and product markets. Take the construction of large-scale refining and chemical integration projects in China, such as PetroChina, Sinopec, Hengli Petrochemical, Zhejiang Petrochemical, Zhongke Petrochemical, and Guangdong Petrochemical as examples. The project sites are mainly concentrated in the southeastern coastal area. This region has unique geographical and environmental advantages, but also puts forward higher requirements for surface corrosion protection of petrochemical equipment and pipelines. According to surveys and statistics, the atmospheric corrosion environment assessment of large petrochemical enterprises in coastal areas has reached corrosion level C4. The corrosion level C4 refers to those with severe pollution in temperate areas or where chloride plays a significant role, such as polluted urban areas, industrial areas, coastal areas without salt spray or not exposed to the strong action of melting ice salts, moderately polluted atmospheric environments in subtropical and tropical areas. Anti-corrosion on the surface of pipelines and equipment costs a lot of money, but has a short service life, high maintenance costs in the future, and possible quality and safety risks. Therefore, how to improve the anti-corrosion quality of petrochemical equipment and pipelines and reduce anti-corrosion costs during the entire life cycle is an issue worth exploring.
A valve is one of the main pipeline components in the petrochemical industry, and its anti-corrosion directly affects the quality and safe use of the entire pipeline. The on-site surface corrosion situation, causes, and improvement measures of valves used in the petrochemical industry are now discussed to improve the surface anti-corrosion quality of valves (Figure 1). The factors that affect the anti-corrosion quality of valves mainly include the following two aspects. One is the anti-corrosion quality of the valve before leaving the factory, and the other is the storage environment and protection after delivery.
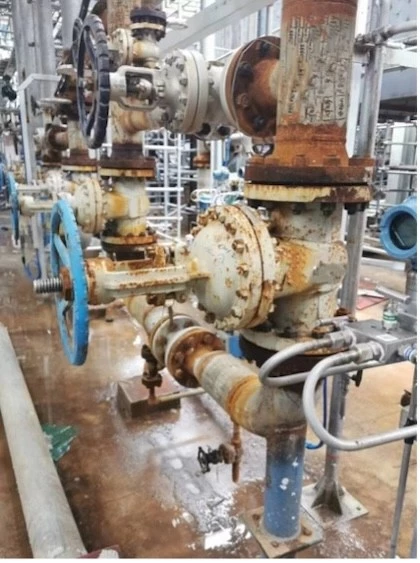
Figure 1 Corroded valves and pipes in service
2. Anti-corrosion of valves before leaving the factory
The anti-corrosion quality of valves before leaving the factory is mainly related to factors such as valve surface treatment, paint selection, painting process, and packaging protection.
(1) Surface treatment of valves
The quality of valve surface treatment directly determines the paint adhesion. It is one of the key factors in the anti-corrosion quality of the valve and is the main cause of paint peeling and rust on the valve. Most valve manufacturers have experienced paint peeling and rust due to poor surface treatment quality. In view of this, two common solutions for valve surface treatment are proposed, which can be used to effectively improve paint adhesion and reduce rust.
The petrochemical industry is the pillar industry in China. Most large petrochemical companies have been built in coastal areas in recent years due to raw material transportation and product markets. Take the construction of large-scale refining and chemical integration projects in China, such as PetroChina, Sinopec, Hengli Petrochemical, Zhejiang Petrochemical, Zhongke Petrochemical, and Guangdong Petrochemical as examples. The project sites are mainly concentrated in the southeastern coastal area. This region has unique geographical and environmental advantages, but also puts forward higher requirements for surface corrosion protection of petrochemical equipment and pipelines. According to surveys and statistics, the atmospheric corrosion environment assessment of large petrochemical enterprises in coastal areas has reached corrosion level C4. The corrosion level C4 refers to those with severe pollution in temperate areas or where chloride plays a significant role, such as polluted urban areas, industrial areas, coastal areas without salt spray or not exposed to the strong action of melting ice salts, moderately polluted atmospheric environments in subtropical and tropical areas. Anti-corrosion on the surface of pipelines and equipment costs a lot of money, but has a short service life, high maintenance costs in the future, and possible quality and safety risks. Therefore, how to improve the anti-corrosion quality of petrochemical equipment and pipelines and reduce anti-corrosion costs during the entire life cycle is an issue worth exploring.
A valve is one of the main pipeline components in the petrochemical industry, and its anti-corrosion directly affects the quality and safe use of the entire pipeline. The on-site surface corrosion situation, causes, and improvement measures of valves used in the petrochemical industry are now discussed to improve the surface anti-corrosion quality of valves (Figure 1). The factors that affect the anti-corrosion quality of valves mainly include the following two aspects. One is the anti-corrosion quality of the valve before leaving the factory, and the other is the storage environment and protection after delivery.
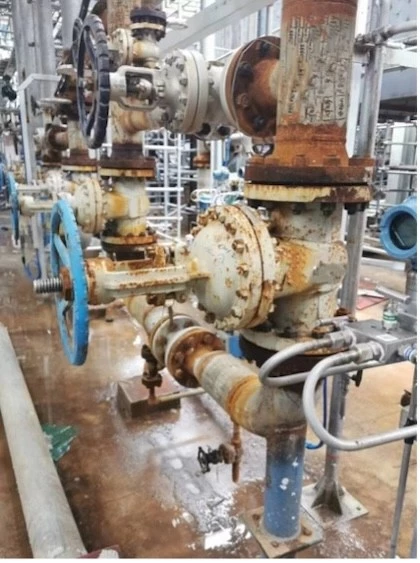
Figure 1 Corroded valves and pipes in service
2. Anti-corrosion of valves before leaving the factory
The anti-corrosion quality of valves before leaving the factory is mainly related to factors such as valve surface treatment, paint selection, painting process, and packaging protection.
(1) Surface treatment of valves
The quality of valve surface treatment directly determines the paint adhesion. It is one of the key factors in the anti-corrosion quality of the valve and is the main cause of paint peeling and rust on the valve. Most valve manufacturers have experienced paint peeling and rust due to poor surface treatment quality. In view of this, two common solutions for valve surface treatment are proposed, which can be used to effectively improve paint adhesion and reduce rust.
a. Organic solvent cleaning: Strict cleaning treatment is carried out before the assembly of the valve and after the hydraulic pressure test. The main cleaning solvent is banana water. Small parts are soaked and brushed. Wash internal and external surfaces of large parts, single valves and complete machines. Valve manufacturers with good capabilities can use ultrasonic cleaning. The steps of ultrasonic cleaning of valves are as follows: cleaning (including partial cleaning) → rinsing (water with a temperature of 50°C to 60°C plus cleaning agent) → rinsing (water with a temperature of 50°C to 60°C) → drying. Visually inspect the appearance of the valve after cleaning. Painting can be carried out only after the cleanliness and appearance meet the requirements.
b. Shot blasting: After the valve pressure test is qualified, the entire valve will be shot blasted to protect the valve stem, studs, nuts and other positions to prevent damage to surfaces. The diameter of the shot should not be greater than 1.5 mm; the surface of shot blasting treatment is required to reach Sa2.5. Parts that are not convenient for shot blasting should be derusted by hand or power tools, and the surface should reach Sa3, that is, when observed without magnification, the surface of the steel should be free of visible oil, grease and dirt, and there should be no adhered oxide scale, rust coatings and foreign impurities.
(2) Selecting painting
The selection of paint mainly considers factors such as the atmospheric environment, operating temperature and material of valves, design life, economy and whether it is heat-insulated (cold-insulated).
(3) Packaging of products
The products are separately packed mainly based on the valve body materials, product specifications, drive forms and customer requirements. The overall requirements are mainly based on the principles of being waterproofing, moisture-proof, and collision resistant. Generally speaking, valves should be packed according to the unit weight and the weight that the box can bear; they should be packed separately according to different materials; the end faces of the valves should be matched with plugs of corresponding specifications to prevent end face from collisions; each valves need to be placed with bags of desiccant, wrapped and sealed with plastic film (plastic bags), and then wrapped with cotton cloth. Small-diameter valves of DN10 to DN50 can be packed in multiple layers, but each layer should be separated by wooden boards; valve manufacturers with good capability can use a foaming machine for packaging. For electric, pneumatic, pneumatic and hydraulic valves with actuators, the actuator should be fixed and supported separately, and the actuators should be placed in wooden boxes to prevent rain and damage to the actuators. For valves with stem extension and no operating mechanism, there should be a circular closed space and the valve stem extension rod should be protected by a cover, and should be placed in a wooden box to be fixed separately or shipped with separate notes. Finally, after the valves are packed, steel belts should be tied around the outside of the wooden box, and information such as being moisture-proofing, no inversion, center of gravity, no stacking, and recommended lifting positions should be marked on the outside of the box.
3. On-site storage and protection
The storage environment and storage protection of the valve when it arrives is another important link that affects the anti-corrosion quality of the valve. There are mainly the following factors:
(1) Climate and environmental factors: Since most project locations are mainly concentrated in the southeastern coastal area, the environmental humidity, temperature, and salinity are relatively high, coupled with intensive rainwater. If the paint is improperly selected, the surface corrosion of the valve will be accelerated and aggravated.
(2) On-site acceptance, storage, and custody: According to the on-site acceptance and storage conditions of large projects in recent years, most valves are stored in the open air, as shown in Figure 2. During on-site acceptance, most valves are subjected to the pressure test one by one, except for welded end valves. After unpacking and visual inspection, the valve is subjected to the pressure test. After the pressure test is qualified, the valve is not effectively protected. There is water accumulation inside the valve cavity. The valve is then placed in the open air, which causes the valve to corrode.
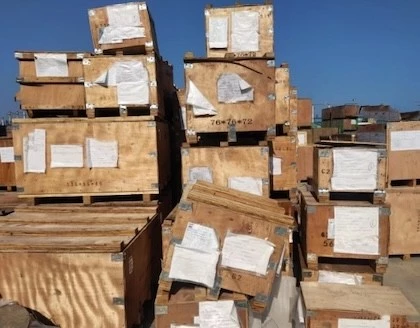
Figure 2 On-site valve storage
(2) Selecting painting
The selection of paint mainly considers factors such as the atmospheric environment, operating temperature and material of valves, design life, economy and whether it is heat-insulated (cold-insulated).
(3) Packaging of products
The products are separately packed mainly based on the valve body materials, product specifications, drive forms and customer requirements. The overall requirements are mainly based on the principles of being waterproofing, moisture-proof, and collision resistant. Generally speaking, valves should be packed according to the unit weight and the weight that the box can bear; they should be packed separately according to different materials; the end faces of the valves should be matched with plugs of corresponding specifications to prevent end face from collisions; each valves need to be placed with bags of desiccant, wrapped and sealed with plastic film (plastic bags), and then wrapped with cotton cloth. Small-diameter valves of DN10 to DN50 can be packed in multiple layers, but each layer should be separated by wooden boards; valve manufacturers with good capability can use a foaming machine for packaging. For electric, pneumatic, pneumatic and hydraulic valves with actuators, the actuator should be fixed and supported separately, and the actuators should be placed in wooden boxes to prevent rain and damage to the actuators. For valves with stem extension and no operating mechanism, there should be a circular closed space and the valve stem extension rod should be protected by a cover, and should be placed in a wooden box to be fixed separately or shipped with separate notes. Finally, after the valves are packed, steel belts should be tied around the outside of the wooden box, and information such as being moisture-proofing, no inversion, center of gravity, no stacking, and recommended lifting positions should be marked on the outside of the box.
3. On-site storage and protection
The storage environment and storage protection of the valve when it arrives is another important link that affects the anti-corrosion quality of the valve. There are mainly the following factors:
(1) Climate and environmental factors: Since most project locations are mainly concentrated in the southeastern coastal area, the environmental humidity, temperature, and salinity are relatively high, coupled with intensive rainwater. If the paint is improperly selected, the surface corrosion of the valve will be accelerated and aggravated.
(2) On-site acceptance, storage, and custody: According to the on-site acceptance and storage conditions of large projects in recent years, most valves are stored in the open air, as shown in Figure 2. During on-site acceptance, most valves are subjected to the pressure test one by one, except for welded end valves. After unpacking and visual inspection, the valve is subjected to the pressure test. After the pressure test is qualified, the valve is not effectively protected. There is water accumulation inside the valve cavity. The valve is then placed in the open air, which causes the valve to corrode.
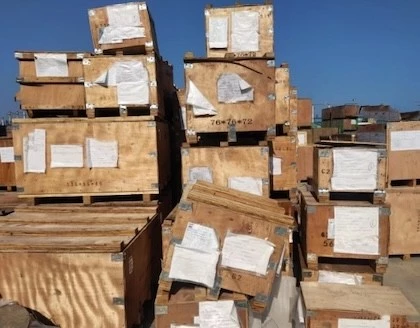
Figure 2 On-site valve storage
Previous: Structural Features of Double Shut-off Plug Valves
Next: Problems and Measures in High Sulfur Natural Gas Field Valves (Part One)