An Introduction to Control Valves
Jul 29, 2024
On this page
Control valves are key components in modern industrial automation and control systems. Their main function is to control the operating state of the entire system by adjusting parameters such as fluid flow, pressure, and temperature. They are widely used in control systems across the fields of petroleum, chemical industry, electric power, metallurgy, and light industry. When selecting a control valve, you should choose the appropriate one based on medium parameters (pressure and temperature), flow, medium characteristics, and the function of the valve, and understand its basic structure and characteristics.
The control valve adjusts the flow of the medium by receiving a signal from the controller and changing the valve opening, thereby controlling the pressure, temperature, liquid level, and other parameters of the system. A control valve generally consists of an actuator and a valve body. The actuator converts the control signal into mechanical motion, drives the valve core in the valve body to move, and thus adjusts the valve opening.
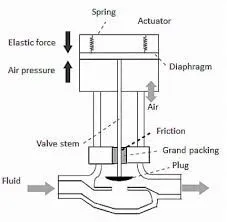
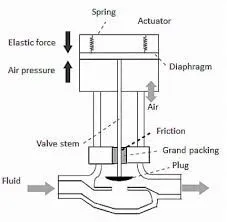
According to different classification standards, control valves can be divided into the following types: According to the mode of action, control valves are divided into electric control valves, pneumatic control valves, and hydraulic control valves. According to the valve body structure, control valves are classified as single-seat valves, double-seat valves, and butterfly valves. According to control characteristics, control valves are classified as linear control valves, equal percentage control valves, and quick opening control valves.
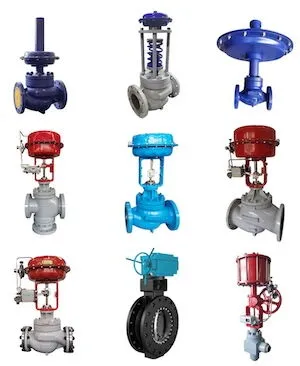
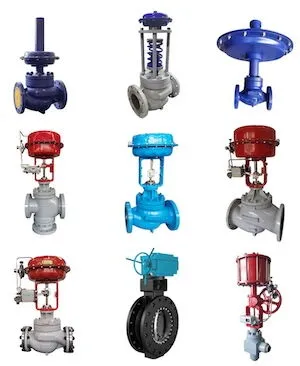
Selecting a suitable control valve requires consideration of many factors, including the nature of the medium, working pressure and temperature, flow characteristics, control accuracy, and other relevant factors. The following are some key points to consider when selecting a control valve:
Medium properties: The valve body material and sealing form need to be selected according to the corrosiveness, viscosity, solid content, and other properties of the medium.
Working conditions: Choose the appropriate valve type and specification based on the working pressure and temperature of the system.
Flow characteristics: Choose the appropriate control characteristics (such as linear, equal percentage, or quick opening) based on the control requirements of the system.
Control accuracy: Consider the sensitivity, response speed, and stability of the control valve to ensure the control accuracy and reliability of the system.
Medium properties: The valve body material and sealing form need to be selected according to the corrosiveness, viscosity, solid content, and other properties of the medium.
Working conditions: Choose the appropriate valve type and specification based on the working pressure and temperature of the system.
Flow characteristics: Choose the appropriate control characteristics (such as linear, equal percentage, or quick opening) based on the control requirements of the system.
Control accuracy: Consider the sensitivity, response speed, and stability of the control valve to ensure the control accuracy and reliability of the system.
As a key component in industrial process control systems, the performance and reliability of control valves directly affect both production efficiency and safety. Therefore, the maintenance of control valves is crucial. The maintenance of control valves includes regular inspection, maintenance, and handling common faults.
Regular inspection and maintenance include appearance checks, functional testing, and sealing inspections. Check the valve’s appearance regularly to ensure there is no leakage, corrosion, cracks, or other obvious damage. Remove dust, oil, and other impurities from the surface of the valve to prevent them from affecting normal operation. Operate the control valve regularly to ensure it opens and closes normally and moves flexibly without sticking. Calibrate the positioner to ensure it accurately feeds back the valve position and makes necessary adjustments. Check the sealing performance of the valve to ensure there is no internal or external leakage. Check the wear on the packing and sealing rings and replace them if necessary. Disassemble the valve regularly and clean internal parts, such as the valve core and valve seat, to prevent dirt accumulation from affecting valve performance. Based on the type of valve and its use, add lubricant as needed to ensure the flexibility of the valve stem and other components. Check the filter, pressure-reducing valve, and air pipe of the air source system to ensure the air source is clean and the pressure is stable. Regularly drain the accumulated water and impurities from the pneumatic actuator. Check the electrical connections and control system of the electric actuator to ensure there is no looseness, short circuit, or other electrical faults. Check and calibrate the positioner and limit switch to ensure they are accurate and sensitive. Clean or replace the pressure-reducing valve and filter to ensure their normal operation.
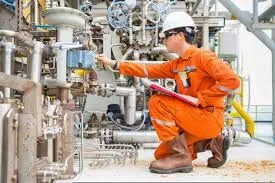
Common faults include internal and external leakage, inflexible movement, and positioner failure. The causes of internal and external leakage are damaged sealing surfaces, aging packing, or improper installation. The seals should be replaced, and damaged parts should be reinstalled or repaired. The causes of inflexible movement are foreign matter between the valve stem and the valve seat, insufficient lubrication, or deformation of the valve stem. Foreign matter should be removed, lubricant should be added, and deformed parts should be replaced. Causes of positioner failure include insufficient air source, miscalibration of the positioner, or electrical failures. The air source should be checked, the positioner should be recalibrated, and electrical failures should be repaired.
Regular inspection and maintenance include appearance checks, functional testing, and sealing inspections. Check the valve’s appearance regularly to ensure there is no leakage, corrosion, cracks, or other obvious damage. Remove dust, oil, and other impurities from the surface of the valve to prevent them from affecting normal operation. Operate the control valve regularly to ensure it opens and closes normally and moves flexibly without sticking. Calibrate the positioner to ensure it accurately feeds back the valve position and makes necessary adjustments. Check the sealing performance of the valve to ensure there is no internal or external leakage. Check the wear on the packing and sealing rings and replace them if necessary. Disassemble the valve regularly and clean internal parts, such as the valve core and valve seat, to prevent dirt accumulation from affecting valve performance. Based on the type of valve and its use, add lubricant as needed to ensure the flexibility of the valve stem and other components. Check the filter, pressure-reducing valve, and air pipe of the air source system to ensure the air source is clean and the pressure is stable. Regularly drain the accumulated water and impurities from the pneumatic actuator. Check the electrical connections and control system of the electric actuator to ensure there is no looseness, short circuit, or other electrical faults. Check and calibrate the positioner and limit switch to ensure they are accurate and sensitive. Clean or replace the pressure-reducing valve and filter to ensure their normal operation.
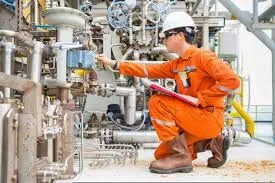
Common faults include internal and external leakage, inflexible movement, and positioner failure. The causes of internal and external leakage are damaged sealing surfaces, aging packing, or improper installation. The seals should be replaced, and damaged parts should be reinstalled or repaired. The causes of inflexible movement are foreign matter between the valve stem and the valve seat, insufficient lubrication, or deformation of the valve stem. Foreign matter should be removed, lubricant should be added, and deformed parts should be replaced. Causes of positioner failure include insufficient air source, miscalibration of the positioner, or electrical failures. The air source should be checked, the positioner should be recalibrated, and electrical failures should be repaired.
As an important part of the industrial automation control system, the performance and reliability of the control valve directly affect the overall effectiveness of the system. By correctly selecting, installing, and maintaining the control valve, the control accuracy and stability of the system can be significantly improved, and the safe and efficient operation of the production process can be ensured. Therefore, it is crucial for engineers and technicians to have a thorough understanding of the working principles and application scenarios of control valves.
Previous: Selecting Control Valves for Offshore Oil and Gas Fields
Next: Electric Valves Stem Troubleshooting