ASTM A216 WCB válvula de retención de disco de inclinación API 594 14 pulgadas 600 libras
¿Busca un fabricante confiable de válvula de retención de disco de inclinación ASTM A216 WCB? Nuestras ofertas incluyen una válvula de 14 pulgadas (DN350, 350 MM), con una calificación de 600 LB (PN100) según el estándar API 594. Hecho de acero al carbono fundido duradero, con una cubierta de perno y un extremo de doble brida para una instalación segura.
Categorías
- Revisar válvulas
Etiquetas
Detalles
Válvula de retención de disco de doble brida WCB de tapa perno
Estándar de diseño: API 594
Body Material: Casting Steel, Carbon Steel, A216 WCB
Nominal Diameter: 14 Inch, DN350, 350 MM
Presión: 600 libras
End Connection: Flange End
Cara a cara: API 594
Prueba y prueba: API 598
TILTING DISC CHECK VALVE
A tilting disc check valve, also referred to as a tilt check valve or tilting-disk check valve, features a disc with a central pivot point. This design allows for smooth opening when flow moves forward and prompt closure during flow reversal.
Primarily utilized in agricultural settings, tilting disc check valves find application across various industries where frequent flow reversal occurs.
The disc's aerodynamic properties enable it to remain open once fully engaged, unlike swing check valves that require higher process velocities to maintain openness.
Compared to swing check valves, tilting disc check valves boast a lighter and more compact disc, with its center of gravity positioned closely to the pivot point. Consequently, these valves exhibit lower cracking pressure and reduced pressure drop at lower flow rates. However, their pressure drop increases relative to swing check valves at higher flow rates.
DESIGN CONSIDERATIONS FOR TILTING DISK CHECK VALVES
Installation Orientation
For optimal performance, the tilting disk check valve should be installed horizontally or vertically, with the flow directed upwards. Installation in a downward flow direction may result in the valve opening unintentionally due to gravitational forces acting on the disk. It is imperative for the installer to ensure correct orientation to prevent improper valve closure.
Mitigating Water Hammer
In scenarios where water hammer is a concern, the tilting disk design offers potential mitigation. The low mass of the disk enables rapid closure, preempting the impact of returning pressure waves and reducing the likelihood of slamming shut.
Maintenance Challenges
Unlike swing check valves, which typically feature a bolted cap for ease of maintenance, tilting disk check valves pose greater challenges. Maintenance often necessitates complete valve removal from the system, a process that is both time-consuming and costly due to the valve's split-body construction. However, in situations where swing check valves are susceptible to unauthorized tampering, such as disk removal, the tilting disk design presents a viable alternative.
To facilitate maintenance procedures, designers should incorporate flanges into the valve assembly. Butt weld end configurations are generally discouraged unless breakout flanges are positioned nearby to streamline maintenance efforts.
Shutoff Considerations
The rapid opening and closing action of the disk may pose challenges in achieving tight shutoff, particularly under low-pressure conditions. In such instances, the use of elastomeric seals is advisable to enhance sealing performance and ensure effective shutoff.
Standards Compliance:
Design & Manufactured to API 6D, ASME B16.34 or Equivalent.
P.T Ratings to ASME B16.34
Face to Face Dimensions to API 6D or ASME B16.34
Flanged Ends to ASME B16.5
Butt-weld Ends to ASME B16.25
Valves Marking to MSS SP-25
Inspection&Tested to API 598 or API 6D
Size Ranges from 2-30 Inch
Pressure Ratings from Class 150 to Class 600, PN16 to PN100
Ends Connections in Flanged R.F or RTJ, Butt-weld or Hub Ends
Structured in Two Piece Bolted Body, One Piece Union Pressure Sealed Body
A variety of body and trim material is offered, including carbon steel ASTM A216 WCB, WCC, Low Carbon Steel LCB, LCC, Alloy Steel WC6, WC9, C5, Stainless Steel CF8, CF8M, CF3, CF3M, Duplex & Super Duplex Steel A890 GR.4A,5Aor F51, Special Materials in Monel, Alu. Bronze C95800, 95600 etc. Coatings may be provided for added corrosion or wear resistance. Hard-facing and weld overlays may also be supplied. Seats
Options with metal-to-metal or bubble-tight resilient.
Optional Bypass system, Dashpot & Counter-weight Assembly.
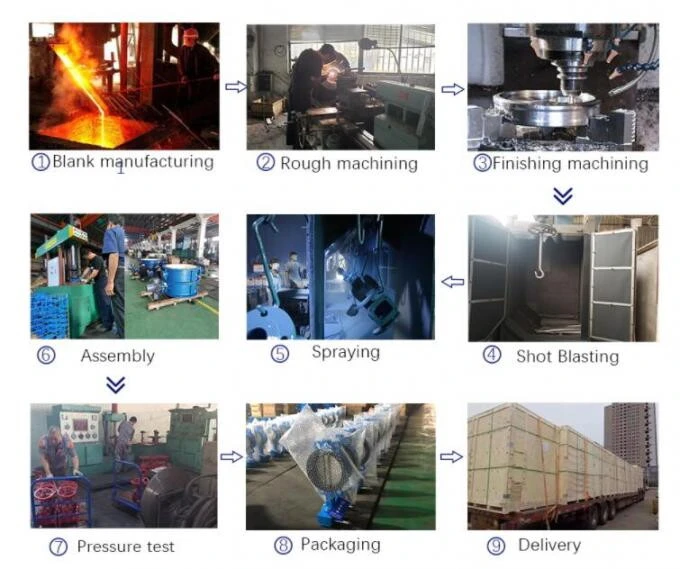
Quality Control
1) Before the order can be confirmed finally, we would strictly check the material, color, and dimension of the sample step by step.
2) We salesman, also as an order follower, would trace every phase of production from the beginning.
3) We have a QC team, every product would be checked by them before being packed.
4) We would try our best to help clients solve problems when they occur.
After Sales Service:
Any small problem happening in our products will be solved at the most prompt time.
We always offer relative technical support.
Quick response, all your inquiries will be replied to within 24 hours.
Estándar de diseño: API 594
Body Material: Casting Steel, Carbon Steel, A216 WCB
Nominal Diameter: 14 Inch, DN350, 350 MM
Presión: 600 libras
End Connection: Flange End
Cara a cara: API 594
Prueba y prueba: API 598
Item | Tilting Disc Check Valve |
Certification | ISO 9001, ISO 14001, ISO 18001, TS, CE, API |
Brand | VERVO |
Model number | H71Y-600LB-DN250 |
Port Size | 14 Inch, DN250, 250mm |
Structure type | Tilting Disc Check Valve |
Pressure | 00LB |
Temperature | -46 - 325℃ |
Connection form | Flanged End |
Material | Casting Steel Carbon Steel A216 WCB |
Feature | Easy disassembly |
TILTING DISC CHECK VALVE
A tilting disc check valve, also referred to as a tilt check valve or tilting-disk check valve, features a disc with a central pivot point. This design allows for smooth opening when flow moves forward and prompt closure during flow reversal.
Primarily utilized in agricultural settings, tilting disc check valves find application across various industries where frequent flow reversal occurs.
The disc's aerodynamic properties enable it to remain open once fully engaged, unlike swing check valves that require higher process velocities to maintain openness.
Compared to swing check valves, tilting disc check valves boast a lighter and more compact disc, with its center of gravity positioned closely to the pivot point. Consequently, these valves exhibit lower cracking pressure and reduced pressure drop at lower flow rates. However, their pressure drop increases relative to swing check valves at higher flow rates.
DESIGN CONSIDERATIONS FOR TILTING DISK CHECK VALVES
Installation Orientation
For optimal performance, the tilting disk check valve should be installed horizontally or vertically, with the flow directed upwards. Installation in a downward flow direction may result in the valve opening unintentionally due to gravitational forces acting on the disk. It is imperative for the installer to ensure correct orientation to prevent improper valve closure.
Mitigating Water Hammer
In scenarios where water hammer is a concern, the tilting disk design offers potential mitigation. The low mass of the disk enables rapid closure, preempting the impact of returning pressure waves and reducing the likelihood of slamming shut.
Maintenance Challenges
Unlike swing check valves, which typically feature a bolted cap for ease of maintenance, tilting disk check valves pose greater challenges. Maintenance often necessitates complete valve removal from the system, a process that is both time-consuming and costly due to the valve's split-body construction. However, in situations where swing check valves are susceptible to unauthorized tampering, such as disk removal, the tilting disk design presents a viable alternative.
To facilitate maintenance procedures, designers should incorporate flanges into the valve assembly. Butt weld end configurations are generally discouraged unless breakout flanges are positioned nearby to streamline maintenance efforts.
Shutoff Considerations
The rapid opening and closing action of the disk may pose challenges in achieving tight shutoff, particularly under low-pressure conditions. In such instances, the use of elastomeric seals is advisable to enhance sealing performance and ensure effective shutoff.
Standards Compliance:
Design & Manufactured to API 6D, ASME B16.34 or Equivalent.
P.T Ratings to ASME B16.34
Face to Face Dimensions to API 6D or ASME B16.34
Flanged Ends to ASME B16.5
Butt-weld Ends to ASME B16.25
Valves Marking to MSS SP-25
Inspection&Tested to API 598 or API 6D
Size Ranges from 2-30 Inch
Pressure Ratings from Class 150 to Class 600, PN16 to PN100
Ends Connections in Flanged R.F or RTJ, Butt-weld or Hub Ends
Structured in Two Piece Bolted Body, One Piece Union Pressure Sealed Body
A variety of body and trim material is offered, including carbon steel ASTM A216 WCB, WCC, Low Carbon Steel LCB, LCC, Alloy Steel WC6, WC9, C5, Stainless Steel CF8, CF8M, CF3, CF3M, Duplex & Super Duplex Steel A890 GR.4A,5Aor F51, Special Materials in Monel, Alu. Bronze C95800, 95600 etc. Coatings may be provided for added corrosion or wear resistance. Hard-facing and weld overlays may also be supplied. Seats
Options with metal-to-metal or bubble-tight resilient.
Optional Bypass system, Dashpot & Counter-weight Assembly.
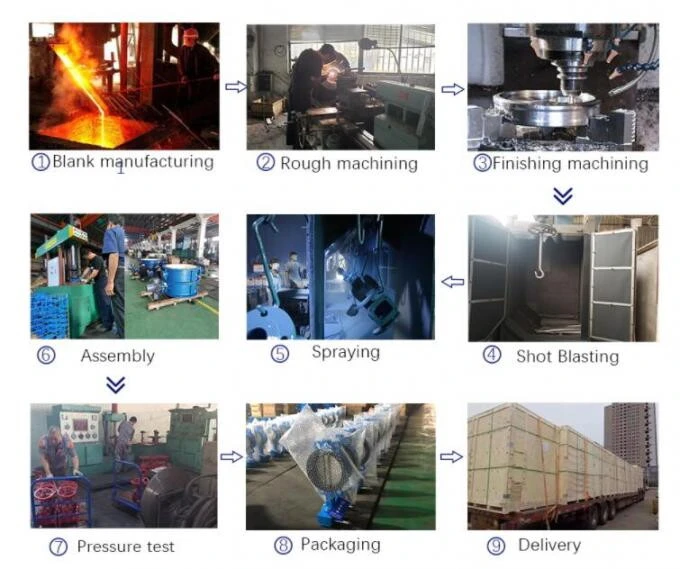
Quality Control
1) Before the order can be confirmed finally, we would strictly check the material, color, and dimension of the sample step by step.
2) We salesman, also as an order follower, would trace every phase of production from the beginning.
3) We have a QC team, every product would be checked by them before being packed.
4) We would try our best to help clients solve problems when they occur.
After Sales Service:
Any small problem happening in our products will be solved at the most prompt time.
We always offer relative technical support.
Quick response, all your inquiries will be replied to within 24 hours.
Siguiente: ASTM A182 F316 válvula de retención de doble placa, 1 pulgada, 150 libras, API 594
Anterior: ASTM A350 LF2 válvula de retención de doble placa, 4 pulgadas, 2500 libras, API 6D